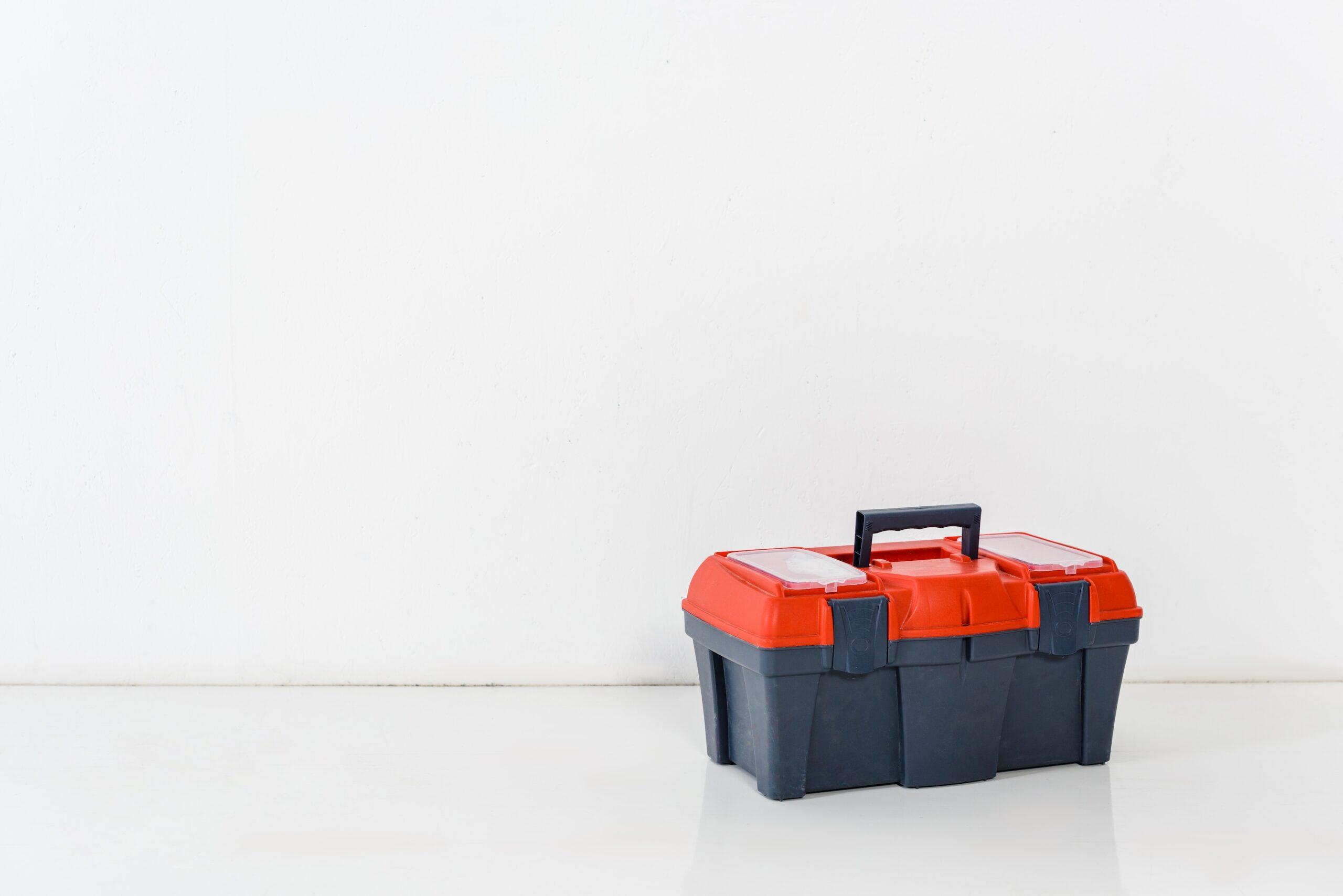
December 13, 2023
Maybe you’re familiar with the five core quality tools – APQP, FMEA, MSA, SPC, and PPAP – but do you truly grasp the intricate dance they perform together?
This blog post will share with you the profound relationship between PPAP and its companions, empowering you to harness their collective power for exceptional quality outcomes.
What is PPAP?
The Production Part Approval Process (PPAP) serves as the final verification that your production parts comply with the specified requirements. It’s essentially a comprehensive documentation package submitted to the customer, showcasing your commitment to quality, and ensuring their confidence in your capabilities.
Now, the crucial question: How does this relate to the other core quality tools?
1. APQP (Advanced Product Quality Planning):
Think of APQP as the foundational blueprint for quality. It meticulously maps out the entire product development and production process, identifying potential risks and establishing a roadmap for mitigation. This meticulous planning ensures a smooth transition from design to production, significantly contributing to the success of PPAP.
2. FMEA (Failure Mode and Effects Analysis):
FMEA acts as the proactive detective, meticulously analyzing potential failure modes in your process and their associated risks. By proactively identifying and addressing these vulnerabilities, you minimize the likelihood of defects, ultimately paving the way for a successful PPAP submission.
3. MSA (Measurement System Analysis):
Imagine a chef meticulously measuring ingredients with an inaccurate scale. No matter how skilled, the results will be inconsistent and disappointing. Similarly, MSA ensures the accuracy and consistency of your measurement systems, guaranteeing the reliability of the data used to assess your parts for PPAP.
4. SPC (Statistical Process Control):
SPC acts as the constant guardian, monitoring your production processes for any deviations from established specifications. By analyzing trends and identifying potential issues early on, you can take corrective actions before they escalate, ensuring the consistent quality of your parts, a crucial component of a successful PPAP submission.
The Power of Synergy:
Each core quality tool plays a vital role in achieving excellence, but the true magic lies in their synergistic interaction. APQP sets the stage, FMEA identifies potential challenges, MSA ensures accurate data, and SPC monitors the process.
Finally, PPAP serves as the culmination of these efforts, presenting a comprehensive picture of your quality management system. Understanding this intricate relationship empowers you to:
- Improve the efficiency and effectiveness of your quality management system.
- Reduce rework and scrap, saving time and resources.
- Enhance customer satisfaction and build stronger relationships.
- Gain a competitive edge in the marketplace.
Remember, mastering the core quality tools is not just about fulfilling requirements, it’s about embracing a culture of continuous improvement. By diligently applying these tools and understanding their interconnectedness, you can unlock the doorway to exceptional quality and achieve remarkable results.
Let's talk to see how PPAP Manager can help your company to save time and money.