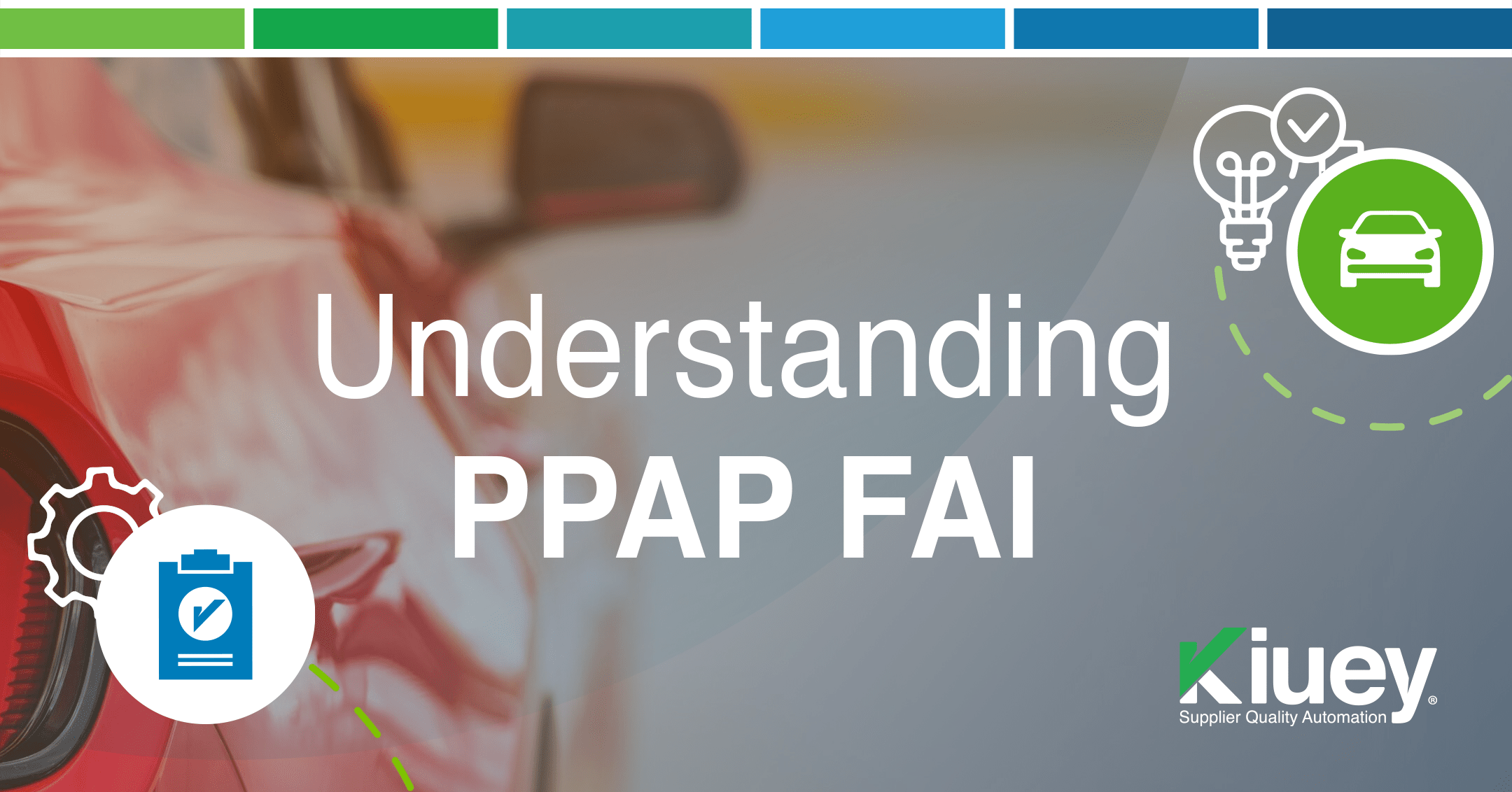
April 26, 2024
As a Supplier Quality Engineer, understanding FAI and PPAP is crucial for ensuring smooth product launches and meeting customer requirements. This guide will equip you with the knowledge to navigate these processes effectively.
What is a First Article Inspection (FAI)?
An FAI is a quality check to verify if your manufacturing process can consistently produce parts that meet specifications. It involves a thorough review of:
- Engineering documentation: This includes drawings, bills of materials, and any relevant design details.
- Manufacturing process: Every step from raw material conversion (machining, molding, etc.) to special processing (plating, hardening, etc.) is examined.
- Functionality: A single part is inspected and tested to ensure it functions as intended.
Benefits of FAI for Suppliers:
- Early identification of issues: Catch design errors or manufacturability problems before mass production.
- Process improvement: Refine your manufacturing process for optimal efficiency and quality.
- Documentation review: Ensure completeness and accuracy of all necessary documents.
When is it required?
- New Product Introduction (NPI): This is a must-have for any new product you’re manufacturing.
- Changes: Any modification to the design, manufacturing process, suppliers, or production after a long pause necessitates a new FAI.
Partial vs. Full:
The extent of the FAI depends on the change. A completely new process or significant design alteration requires a full FAI with a new part. Minor changes, like a new powder coating process, might only warrant a partial FAI focusing on the impacted aspects.
What’s the Difference?
While FAI is a crucial step, PPAP is a broader process encompassing FAI. PPAP involves additional requirements like:
- Production run: PPAP typically involves producing tens to hundreds of parts to assess production rate and process capability.
- Detailed Documentation: PPAP requires formalized documentation for every stage of NPI, including quality control plans, potential failure mode analyses, and process flow diagrams.
Understanding Raw Material Records
The buyer will specify the raw material requirements. You, as the supplier, need to provide certificates of conformance (CoC) from the mill, proving the materials meet specifications. These CoCs typically include details like mill name, material grade, and test results.
The Importance of Dimensional Records
Dimensional records document how well the part meets specified dimensions. This includes both pass/fail checks and precise measurements. Remember, these measurements must be traceable to calibrated gauges, ensuring accuracy and repeatability.
Conclusion
By mastering FAI and PPAP processes, you can streamline communication with customers, ensure product quality, and gain a competitive edge. Remember, FAI is a subset of PPAP, focusing on a single part and core documentation. Leverage this knowledge to excel in your role as a Supplier Quality Engineer!
Let's talk to see how PPAP Manager can help your company to save time and money.