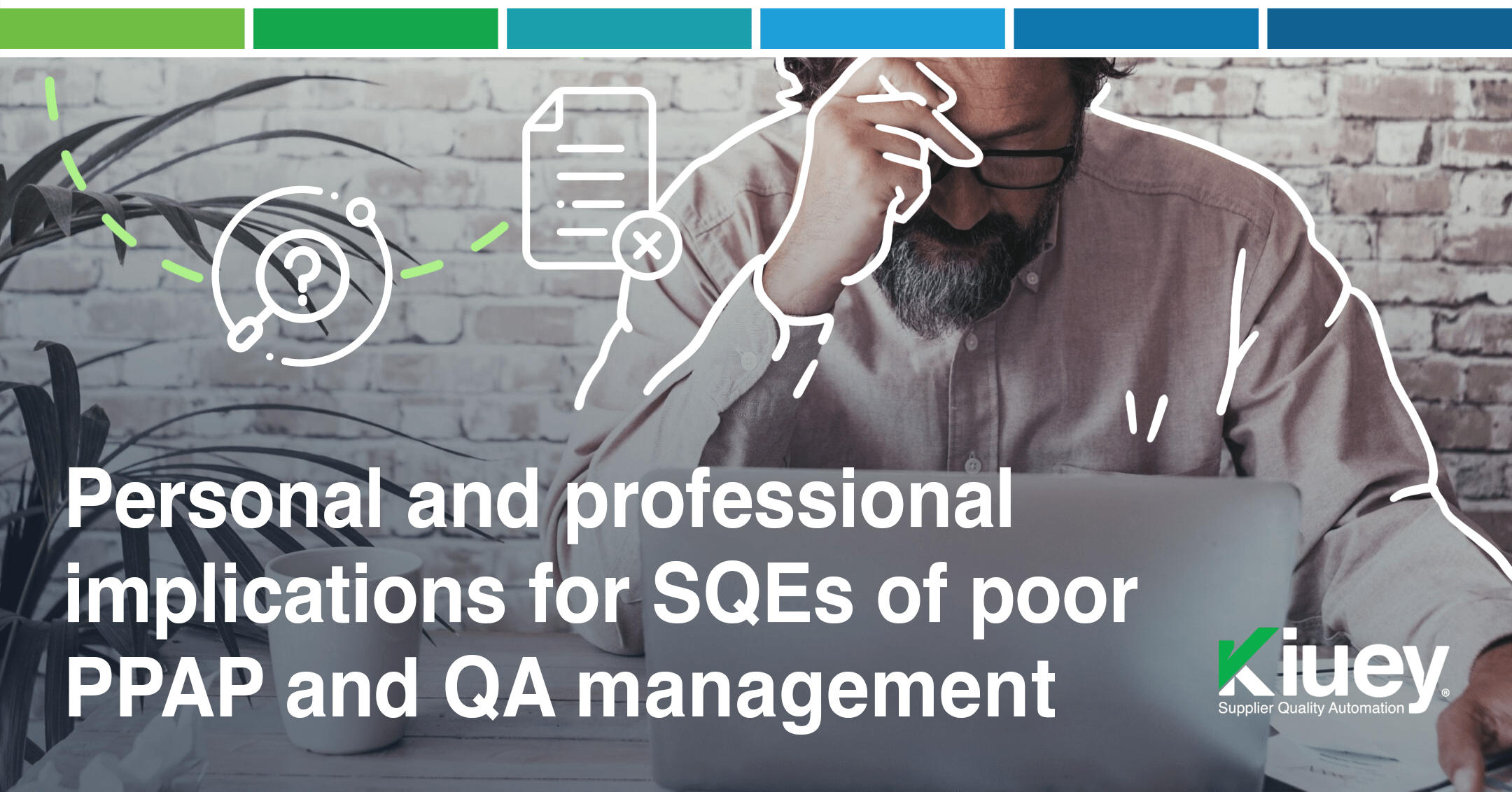
May 16, 2024
Ineffective PPAP management and lax quality assurance (QA) processes can lead to a cascade of issues, disrupting the supply chain and impacting product quality. Let’s delve into the common pitfalls that cause these problems.
Diagnosing the Problems: Common Scenarios
This is the first step to start addressing the issues. How can you identify that something no-so-good is happening and it can eventually impact deeper on personal and professional terms?
On more than one occasion, the problem originates from inadequate communication. It’s in some sort of way known that communication is one of the big problems within organizations, and the manufacturing environment is no different.
Either it’s by language, cultural or knowledge-related barriers, poor communication arises constantly between suppliers, engineers and production teams, causing delays and missed crucial information.
Putting on a common scenario, a simple but great example is when a supplier quality manager, based on the US, requires its SQ team to meet online upon a certain hour, but:
- One of them lacks technological abilities and does not know how to effectively connect to the Zoom meeting.
- The other one is right now living on Asia and does not fits the hour span of the team working from US.
- The last one does not speaks English too well.
You can already imagine that this will deliver into a complex context. This may sooner or latter deliver into an scenario in which it’s unclear if the guidelines for documentation (PPAP) and quality checks are correct, and this can evolve to confusion and inconsistencies.
Also, this lack of communication can eventually transform into “heavy problems” such as the misconception of standards and procedures or the persistence of limited resources that are not well communicated; this can hinder effective PPAP management and QA.
Impact on SQEs
All these past causes can affect SQEs professionally and personally, ultimately delivering into:
- Increased workload due to rework and resolving supplier discrepancies caused by unclear PPAP requirements.
- Pressure to expedite approvals due to lack of communication or delays in the PPAP process.
- Frustration and stress managing issues arising from inadequate training or limited resources.
Addressing solutions
Given the impact, the next step is to hop on actionable steps to improve PPAP management and QA processes, guided through the communication enhancement, methodological and channel-wise speaking, between all the stakeholders:
- Standardization: Implementing clear and consistent PPAP documentation procedures.
- Comprehensive Training: Providing SQEs with proper training on PPAP and best practices for quality control.
- Resource Allocation: Ensuring adequate manpower and equipment to handle PPAP and QA tasks effectively.
This way, improved PPAP management and QA will ultimately deliver into:
- Reduced rework and improved product quality.
- Streamlined production process and increased efficiency.
- Reduced stress and improved work-life balance for SQEs.
There are a lot of examples and case studies that can be found over the Internet to depict the potential outcome of poor PPAP management as well as the personal and professional implications of what this can generate within quality assurance colleagues. However -in all of them- stepping up for a solution implies following the industry’s best practices, as well as a lot of communication-based improvements (moreover in these times, when collaboration is partly remote) that can overall leverage the production process and deliver high-quality products.
If you want to nurture and improve your PPAP management process, don’t hesitate to contact us and schedule your demo; we are sure we can help in the way.
Let's talk to see how PPAP Manager can help your company to save time and money.