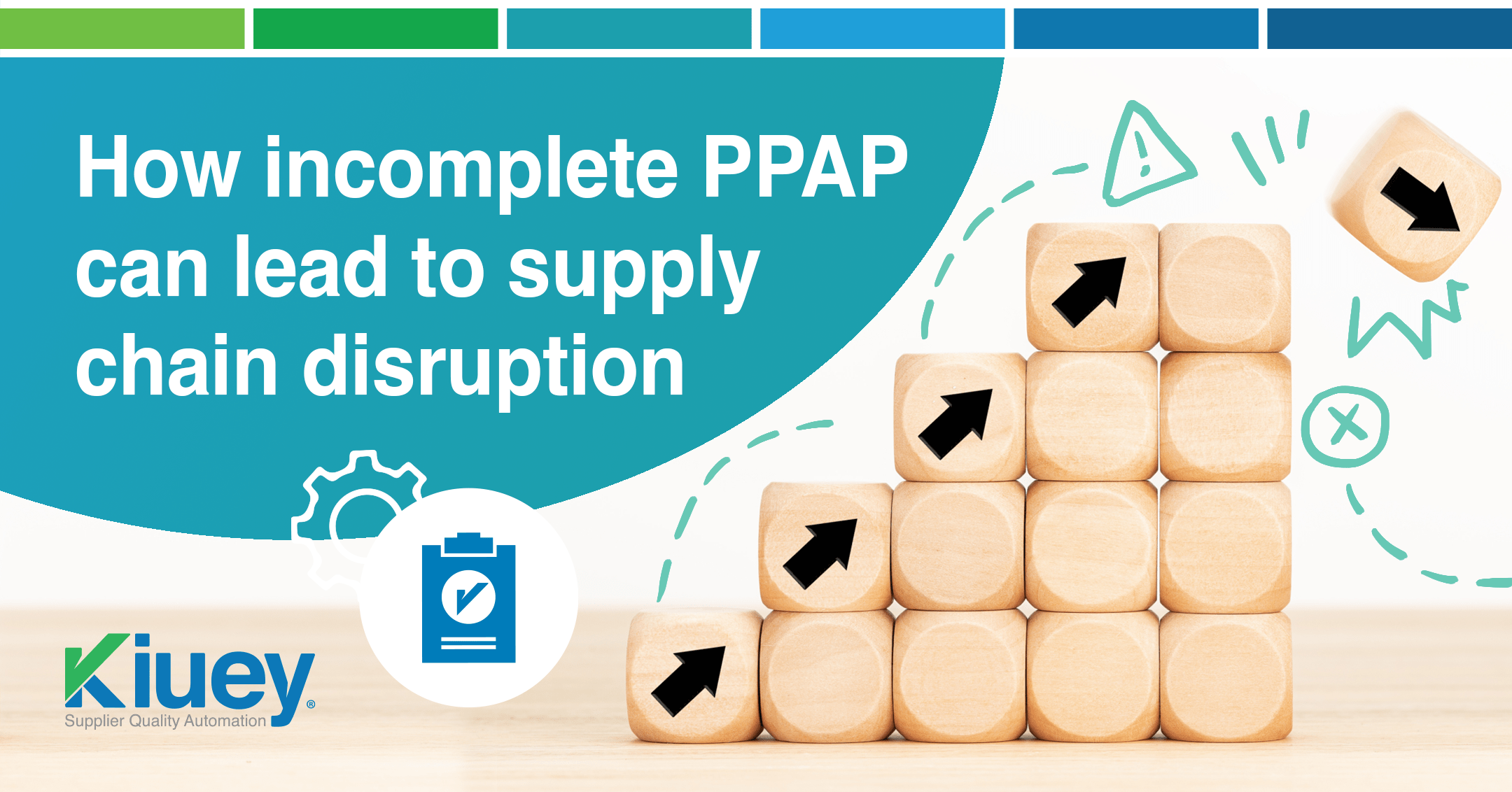
May 8, 2024
There can be several negative consequences of not managing the Production Part Approval Process (PPAP) correctly; this can eventually scale up to a supply chain disruption.
Overall, an incorrect or incomplete PPAP documentation can lead to issues between a manufacturer and its suppliers.
This can disrupt the supply chain and make it difficult to get the parts needed for production, eventually delivering to delayed productions, poor quality products, and increased costs, as well as a costly reputation crisis.
A cause-based illustrative example of supply chain disruption
Let’s imagine a scenario where a company, Mega Motors, builds motorcycles. They rely on a specific type of fuel injector from a supplier, Spark Plug Co. Mega Motors has a strict PPAP process in place.
One day, Spark Plug Co. makes a minor change to the internal design of the fuel injector to improve efficiency. They believe this change is insignificant and won’t affect functionality. However, in their haste to get the new injectors into production, they neglect to update the PPAP documentation with Mega Motors.
Mega Motors receives the new injectors and starts incorporating them into their motorcycles. Unfortunately, the seemingly minor design change causes the injectors to vibrate slightly more than before. This vibration over time loosens a key connection within the Mega Motors engine, leading to oil leaks.
Mega Motors starts receiving customer complaints about oil leaks. They investigate and discover the correlation with the new fuel injectors. The problem is that since Spark Plug Co. never submitted updated PPAP documents, Mega Motors had no way of knowing about the design change and its potential consequences.
This throws Mega Motors into a scramble. They must halt production using the new injectors, investigate the issue, and work with Spark Plug Co. to get the proper PPAP documentation submitted. In the meantime, their production line is stalled, and they can’t fulfill customer orders.
Stepping up on the resolution towards supply chain disruption
Maybe the past example is a similar story for you. This is a classic example of how a seemingly minor oversight in PPAP management can lead to a significant supply chain disruption.
By following PPAP procedures carefully, manufacturers can avoid these problems and ensure a smooth production process with high-quality products. As a formal and critical process for manufacturing, quality assurance professionals can be guided by its essential checklist basics to meet the requirements of the customers.
Moreover, what’s more important is to have a powerful and fluent tool that can manage PPAPs with ease to reduce time spent on repetitive tasks and enhance productivity over the supply chain. If that’s your case, give yourself a try upon our PPAP Management solution by scheduling your demo today!
Let's talk to see how PPAP Manager can help your company to save time and money.