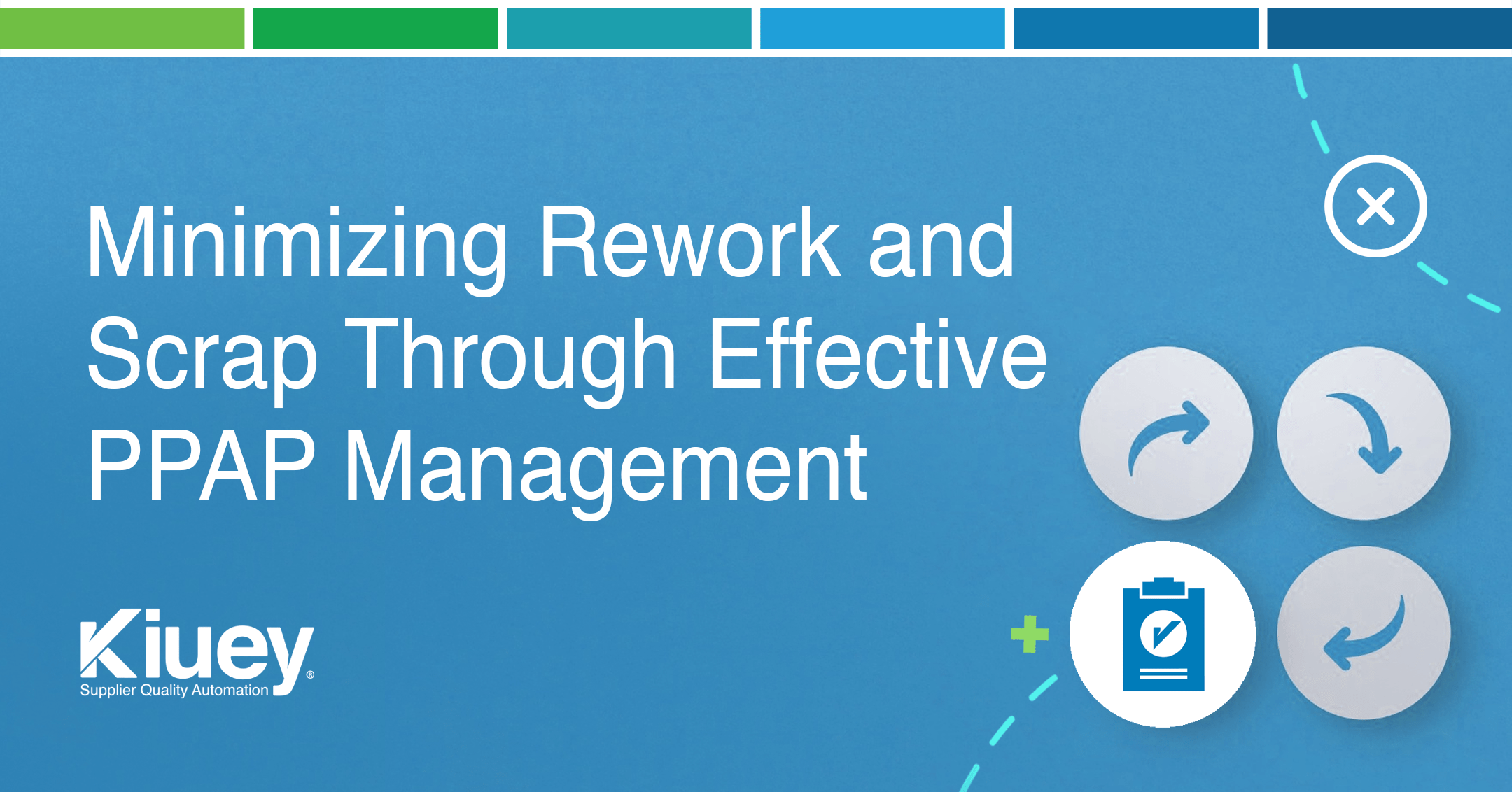
June 20, 2024
Imagine this scenario: a crucial component arrives, ready for integration. The Production team, eager to keep the assembly line humming, rushes the installation. But during final testing, a critical failure emerges. The component doesn’t meet specifications. The line screeches to a halt. A frantic scramble ensues – tracing the issue, contacting the supplier, and potentially having to scrap the entire batch.
This costly scenario, unfortunately, isn’t uncommon. It’s a direct consequence of poorly managed Production Part Approval Process (PPAP). For Supplier Quality Engineers (SQEs), the stakes are high. Ineffective PPAP management translates directly into wasted resources and delays – the very things they’re tasked with preventing. The culprit? Rework and scrap.
The Rework and Scrap Epidemic
Poor PPAP submissions create a breeding ground for these production killers. Here’s how:
- Incomplete Documentation: Missing information, such as Initial Sample Inspection Reports (ISIR) or Process Flow Diagrams (PFDs), leaves the SQE blind to potential issues. Undetected process flaws fester, manifesting as defective parts later in production. These parts require rework – a time-consuming and expensive process of fixing non-conforming components. In worst-case scenarios, the defects are so severe that the parts are deemed scrap, leading to wasted materials and further production delays.
- Inaccurate Data: Discrepancies between documented procedures and the actual manufacturing process are a ticking time bomb. For instance, if the documented gauge calibration frequency doesn’t match the actual practice, undetected equipment drift can create a slow, steady stream of non-conforming parts. Each defective piece necessitates rework or scrapping, eroding production efficiency and profitability.
- Delayed Submissions: Late PPAP submissions disrupt production planning. The OEM might have to hold off on releasing production orders, causing a domino effect of delays. This translates into lost production time and potential missed deadlines. To catch up, manufacturers may resort to rushing production, which can increase the likelihood of errors and further rework.
The SQE’s Anti-Scrap and Rework Arsenal:
So, how can SQEs combat this epidemic of rework and scrap? Here’s their arsenal:
- Standardization and Training: Standardized processes for PPAP submissions within the supplier organization ensure consistency and accuracy. Regular training for both SQEs and supplier personnel on PPAP requirements foster a common understanding of expectations, minimizing the risk of documentation errors that lead to rework.
- Early Engagement: Proactive engagement with suppliers early in the development phase allows SQEs to identify potential issues before they snowball into production problems. Early detection means early correction, preventing rework and scrap later down the line.
- Detailed Review with a Rework and Scrap Lens: Don’t just check for completeness of documentation; scrutinize it with a focus on preventing rework and scrap. Look for gaps in the process that could lead to defects, missing data on control plans, or inadequate quality checks. By anticipating problems, SQEs can ensure the process is set up for success from the outset.
- Focus on Process Capability, Not Just Procedures: Verifying documented procedures is a good start, but it’s not enough. SQEs should demand evidence of process capability through data analysis like control charts. This data provides concrete proof that the process can consistently produce parts within specifications, minimizing the risk of rework and scrap.
- Effective Communication is Key: Maintaining clear and open communication with the supplier throughout the PPAP process is crucial. Addressing discrepancies or concerns promptly prevents misunderstandings that can lead to wasted time and rework loops.
- Continuous Improvement: Regularly reviewing PPAP submissions and identifying areas for improvement is a never-ending cycle. Collaborate with suppliers to implement ongoing process optimization strategies. By constantly refining the manufacturing process, SQEs can minimize the risk of defects and the associated rework and scrap.
A robust PPAP system, spearheaded by proactive SQEs, isn’t just about ticking boxes; it’s about preventing rework and scrap, the silent assassins of production efficiency. By implementing these solutions, SQEs can transform PPAP into a powerful tool for ensuring quality, saving costs, and keeping production lines running smoothly.
Remember, effective PPAP management is an investment in a smoother, more profitable future for everyone involved.
Let's talk to see how PPAP Manager can help your company to save time and money.