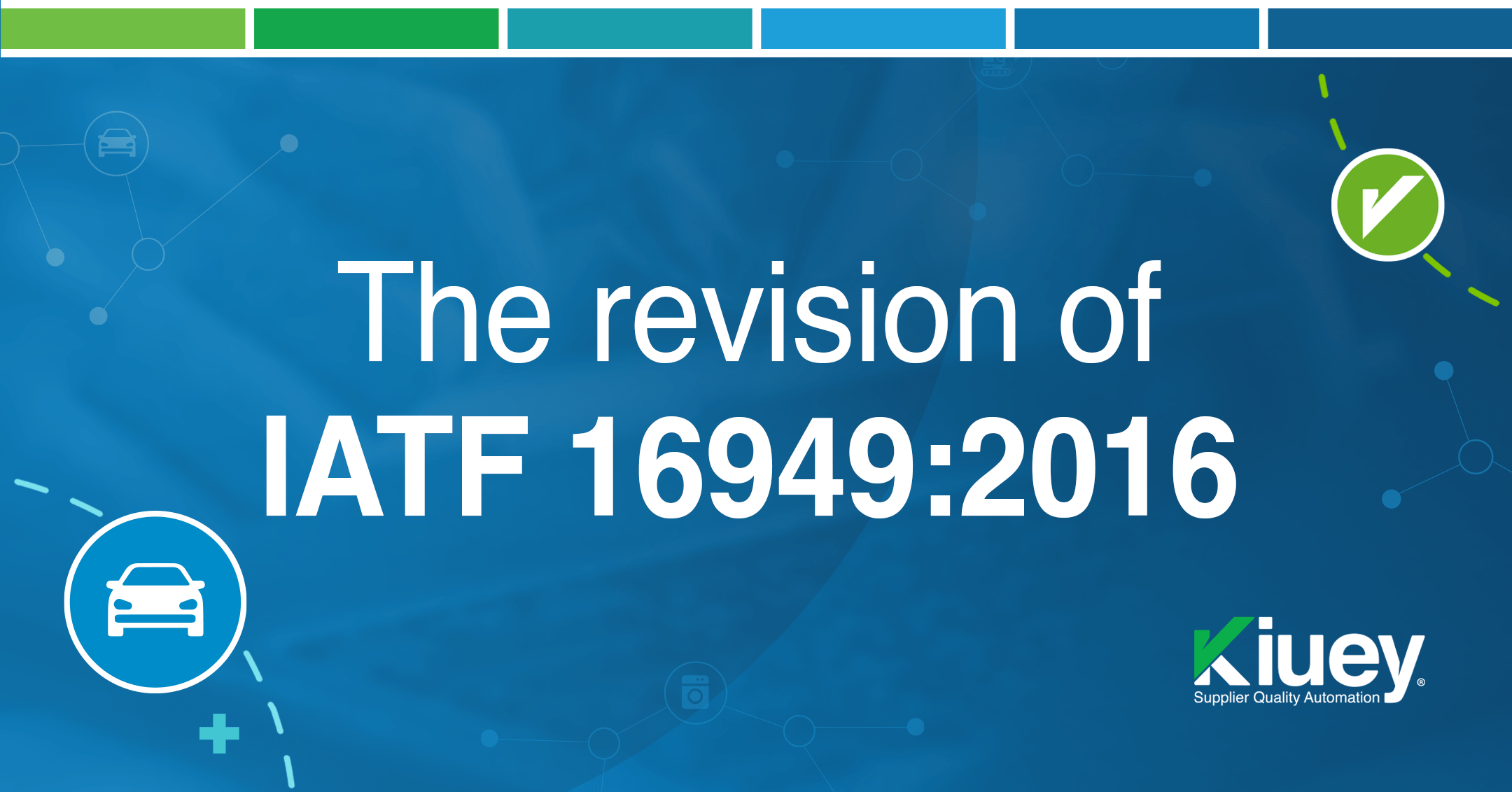
October 26, 2024
On the final days of October 2024, IATF announced that Stakeholder Communiqué SC-2024-006, IATF 16949 Revision 2 has been approved.
The purpose of this Stakeholder Communiqué is to advise all IATF Stakeholders that IATF has started the revision process of the automotive quality management system standard IATF 16949:2016. The details are yet to be depicted when the new version of the standard is released following the publication of the revised ISO 9001.
Why IATF 16949:2016 Matters
IATF 16949:2016 is a globally recognized quality management system standard, designed to help you navigate the complexities of the automotive industry and deliver exceptional results. It’s specifically tailored to the automotive industry, addressing its unique challenges and customer expectations. By adhering to this standard, you can:
- Enhance Product Quality: Implement robust quality management systems to reduce defects and improve product performance.
- Optimize Processes: Streamline operations, eliminate waste, and increase efficiency through lean manufacturing principles.
- Mitigate Risk: Proactively identify and address potential risks to prevent costly recalls and customer dissatisfaction.
- Strengthen Supplier Relationships: Build trust and credibility with your customers by demonstrating your commitment to quality and continuous improvement.
- Gain a Competitive Edge: Differentiate your organization from competitors and attract new business opportunities.
Key Areas of Focus for Supplier Quality Engineers
To effectively implement IATF 16949:2016, supplier quality engineers should focus on the following key areas:
- Customer Requirements:
- Understand and interpret customer specifications, drawings, and other technical documents.
- Ensure that products and services meet or exceed customer expectations.
- Collaborate with customers to identify and address quality issues promptly.
- Supplier Development:
- Evaluate and select suppliers based on their quality management systems and performance history.
- Conduct supplier audits to assess their compliance with IATF 16949:2016 and other relevant standards.
- Provide technical assistance and training to suppliers to improve their capabilities.
- Quality Planning:
- Develop and implement effective quality plans that address potential risks and opportunities.
- Establish clear quality objectives and targets.
- Define key performance indicators (KPIs) to monitor progress and measure success.
- Process Control:
- Monitor and control manufacturing processes to ensure consistency and predictability.
- Utilize statistical process control (SPC) techniques to identify trends and prevent deviations.
- Implement corrective and preventive actions to address quality issues.
- Product Verification and Validation:
- Conduct inspections, tests, and other verification activities to ensure product conformance.
- Validate manufacturing processes to ensure they are capable of producing products that meet specifications.
- Implement effective product traceability systems.
- Continuous Improvement:
- Foster a culture of continuous improvement by encouraging employee involvement and innovation.
- Conduct regular reviews of the quality management system to identify opportunities for improvement.
- Implement corrective actions to address root causes of problems.
By focusing on these key areas and embracing the principles of IATF 16949:2016, supplier quality engineers can play a critical role in driving quality excellence and ensuring the long-term success of their organizations.
Let's talk to see how PPAP Manager can help your company to save time and money.