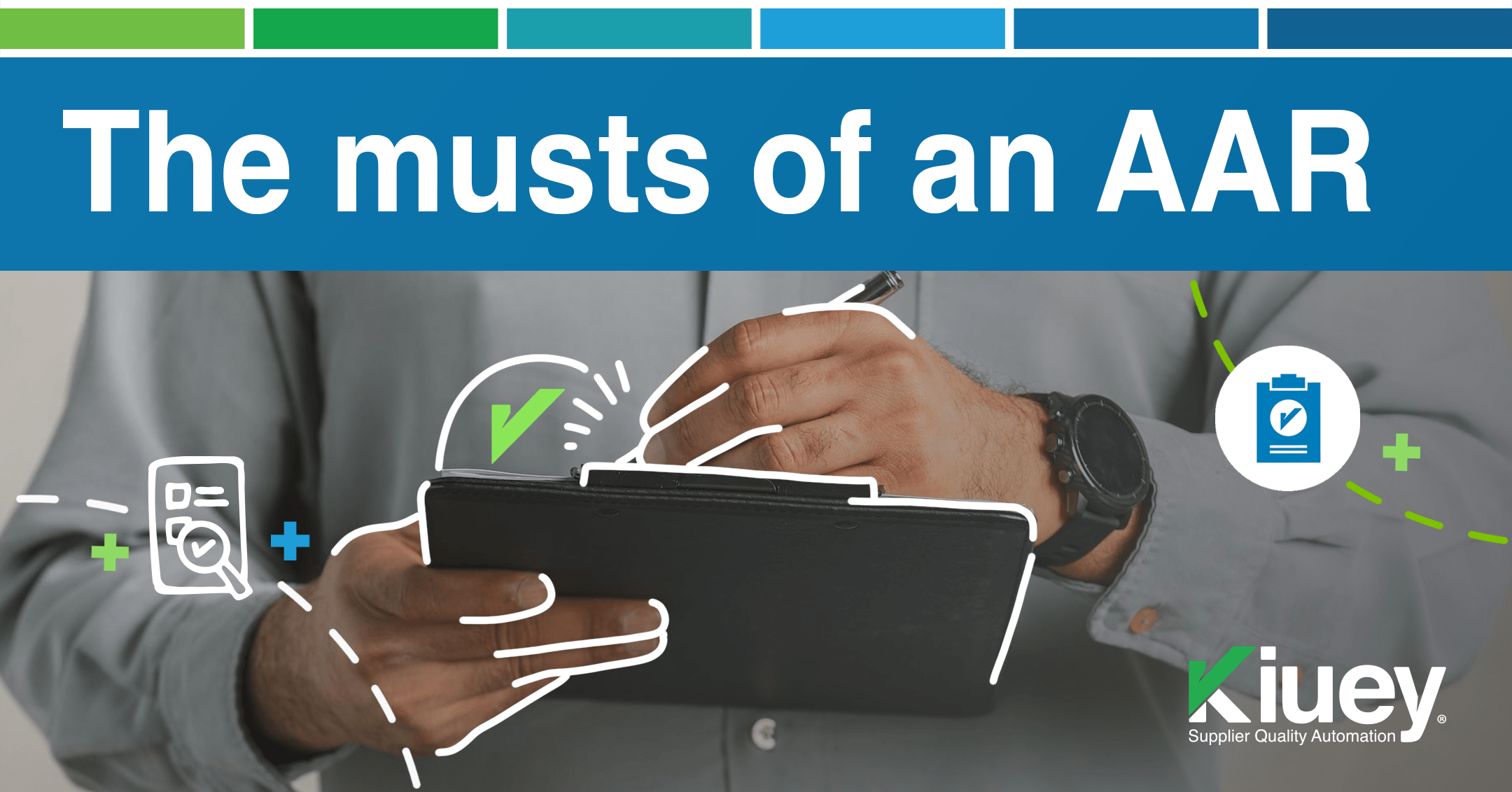
October 11, 2023
As a Supplier Quality Engineer, you are entrusted with guaranteeing that the products your company receives are functional and look impeccable. The Appearance Approval Report (AAR) becomes your secret weapon in industries where aesthetics matter as much as functionality.
Before we plunge into the specifics, let’s understand why the Appearance Approval Report is a critical component of the Production Part Approval Process (PPAP) and how it can significantly benefit you:
- Clarity in Aesthetics: The AAR serves as a visual reference guide, ensuring that the appearance of the supplied parts matches the desired aesthetic standards. This is crucial in industries like automotive, consumer electronics, and cosmetics, where the look and feel of a product are integral to its marketability.
- Quality Assurance: A well-documented AAR helps maintain consistent quality in the appearance of parts. It serves as a supplier benchmark, making it easier to identify and rectify discrepancies promptly.
- Customer Satisfaction: In a world driven by consumer preferences, ensuring that products meet visual expectations is paramount. An accurate AAR ensures that your customers receive products that work flawlessly and look impressive.
- Cost Savings: Preventing visual defects early in production can save substantial costs related to rework, scrap, and customer complaints.
Unpacking the Elements of an Appearance Approval Report:
Now, let’s explore what an AAR should include to fulfill its role effectively:
- Part Identification: Specify the part number, name, and description. Include any relevant drawings or images to aid in identification.
- Appearance Criteria: Detail the specific critical visual characteristics of the part. This could include color, texture, surface finish, and other visual attributes relevant to your industry.
- Sample Part: Provide a sample of the part that serves as the visual reference. Ensure that it represents the desired appearance accurately.
- Inspection Methodology: Explain the methodology and equipment used for inspecting the appearance attributes. This should cover everything from color measurement devices to visual inspection criteria.
- Measurement Results: Document the measurement results for each appearance attribute, ensuring that they align with the specified criteria.
- Photos and Visual Aids: Include clear, high-quality photographs or visual aids that illustrate the appearance attributes and the sample part’s conformity with the criteria.
- Authorized Representative Signature: Like other PPAP documents, the AAR must be signed by an authorized representative, indicating their approval of the visual standards.
In conclusion, the Appearance Approval Report is your tool for achieving visual excellence in the products you receive. It’s not just about ensuring things work; it’s about ensuring they look outstanding, too. By understanding the elements of an AAR and its significance, you can ensure that your company consistently delivers products that meet functional and aesthetic expectations.
Let's talk to see how PPAP Manager can help your company to save time and money.