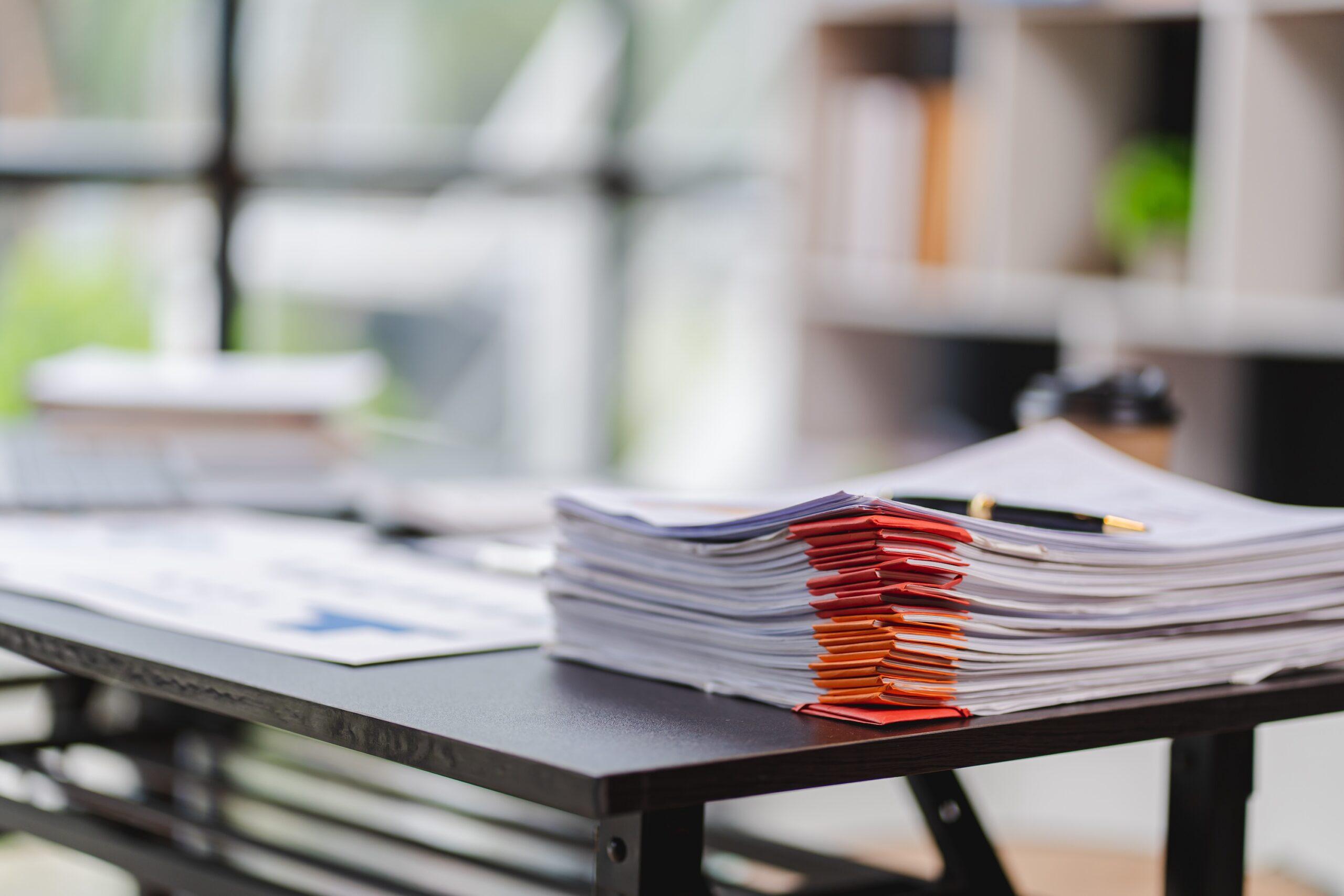
November 8, 2023
Supplier Quality Engineers often find themselves deciphering the enigmatic world of PPAP (Production Part Approval Process) in the labyrinth of quality assurance and production standards. The interim PPAP, though a critical bridge between design and production, harbors its own set of mysteries; given this circumstance, interim PPAP documentation issues can confound even the most adept professionals.
The interim PPAP process acts as a critical juncture, enabling the evaluation of a part’s capability to meet specifications before moving to full production. However, within this crucial phase lies a multitude of interim PPAP documentation issues that can impede the smooth progression of this process.
Let’s delve into these issues and unveil how understanding and addressing them can significantly benefit Supplier Quality Engineers.
Issue 1: Incomplete or Inaccurate Records:
One of the most prevalent problems in interim PPAP documentation is the presence of incomplete or inaccurate records. These errors can stem from various sources, such as missing data, improperly filled forms, or discrepancies between the provided information and the actual part.
Issue 2: Inadequate Information Flow:
Effective communication is the cornerstone of successful interim PPAP processes. However, issues often arise due to inadequate information flow between stakeholders, causing delays, misunderstandings, and ultimately, an impediment to the overall approval process.
Issue 3: Non-Compliance with Standards:
Meeting stringent industry standards is paramount, yet non-compliance is a common stumbling block. Supplier Quality Engineers may grapple with aligning documentation with the required standards, leading to rejection or delays in approvals.
How Understanding These Issues Benefits Supplier Quality Engineers:
Understanding the nuances and intricacies of these interim PPAP documentation issues is akin to holding the master key. It unlocks a multitude of benefits for Supplier Quality Engineers, including:
Enhanced Efficiency:
By recognizing and rectifying documentation errors promptly, you streamline the entire approval process. This results in quicker approvals, reduced lead times, and enhanced operational efficiency.
Improved Communication and Collaboration:
Addressing issues related to information flow fosters improved communication between stakeholders. The clarity in information exchange results in a more collaborative environment, ensuring smoother transitions through the PPAP phases.
Regulatory Compliance and Risk Mitigation:
Comprehending and rectifying non-compliance issues ensures adherence to industry standards and regulations, reducing the risk of rejections and delays, thus safeguarding the organization’s reputation and productivity.
Addressing and Resolving Interim PPAP Documentation Issues
To overcome these documentation challenges, Supplier Quality Engineers must adopt a proactive approach:
- Thorough Review and Verification: Start by conducting a meticulous review of documentation. Verify data accuracy and completeness to rectify any discrepancies before submission.
- Enhance Communication Channels: Establish clear communication channels among stakeholders. Regular meetings, clear guidelines, and updated documentation templates can improve information flow.
- Continuous Training and Adherence to Standards: Invest in continuous training to ensure teams are well-versed with industry standards. Regular audits and internal checks can ensure ongoing compliance.
A Recap and the Road Ahead:
Understanding the complexities of interim PPAP documentation is crucial for Supplier Quality Engineers to navigate this phase effectively.
Addressing these issues leads to enhanced efficiency, collaboration, and compliance, ultimately driving smoother production transitions.
Let's talk to see how PPAP Manager can help your company to save time and money.