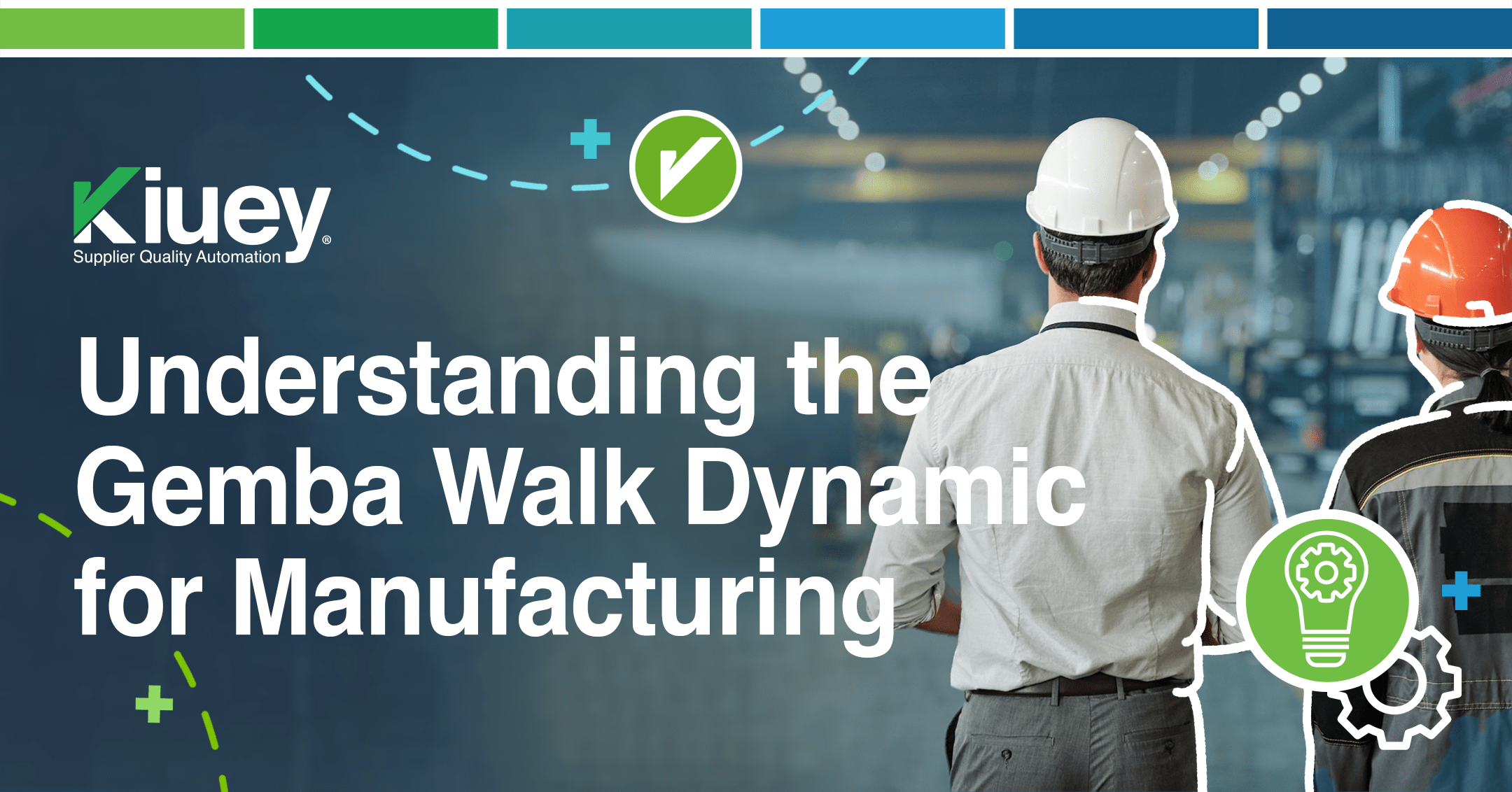
August 28, 2024
A Gemba Walk, a Japanese term meaning “the actual place,” is a structured observation technique used to gain firsthand insights into the actual work environment. In manufacturing, it involves managers or supervisors walking the shop floor to observe processes, talk to employees, and identify areas for improvement. This practice is essential for quality professionals and supplier quality engineers as it provides a direct connection to the source of product quality.
Steps to Conduct a Successful Gemba Walk:
- Define the Purpose: Clearly outline the objectives of the Gemba Walk. Are you looking to identify waste, improve efficiency, or assess supplier performance? A well-defined purpose will guide the focus of the walk.
- Select the Team: Assemble a team of individuals who have a direct connection to the process or supplier being evaluated. This might include quality engineers, process engineers, production supervisors, and representatives from the supplier.
- Prepare Questions: Develop a list of questions to guide the discussion. Consider asking about the process flow, challenges faced, potential improvements, and adherence to quality standards.
- Observe the Process: Walk the shop floor, paying attention to the physical layout, equipment, and the flow of materials. Look for signs of waste, such as excess inventory, waiting time, or unnecessary movement.
- Engage with Employees: Talk to employees involved in the process. Ask them about their roles, challenges, and ideas for improvement. Encourage open communication and active listening.
- Document Findings: Take notes or use a checklist to document your observations and discussions. Capture key points, potential issues, and areas for further investigation.
- Analyze and Act: After the Gemba Walk, review your findings and identify opportunities for improvement. Prioritize actions based on their impact on quality, efficiency, or cost.
- Follow Up: Implement the agreed-upon actions and follow up to ensure they are effective. Schedule follow-up Gemba Walks to assess progress and identify additional areas for improvement.
Key Benefits of Gemba Walks:
- Improved Understanding: Gemba Walks provide a deep understanding of the process and its challenges.
- Enhanced Problem-Solving: By observing the process firsthand, you can identify root causes of issues and develop effective solutions.
- Stronger Relationships: Engaging with employees builds trust and fosters a collaborative work environment.
- Continuous Improvement: Gemba Walks support a culture of continuous improvement by encouraging a data-driven approach to problem-solving.
- Supplier Performance Assessment: For supplier quality engineers, Gemba Walks can be used to assess supplier performance, identify areas for improvement, and strengthen supplier relationships.
By conducting regular Gemba Walks, quality professionals and supplier quality engineers can gain valuable insights, improve process efficiency, and ensure product quality. This practice is essential for driving continuous improvement and achieving organizational excellence – ought to try it?
Let's talk to see how PPAP Manager can help your company to save time and money.