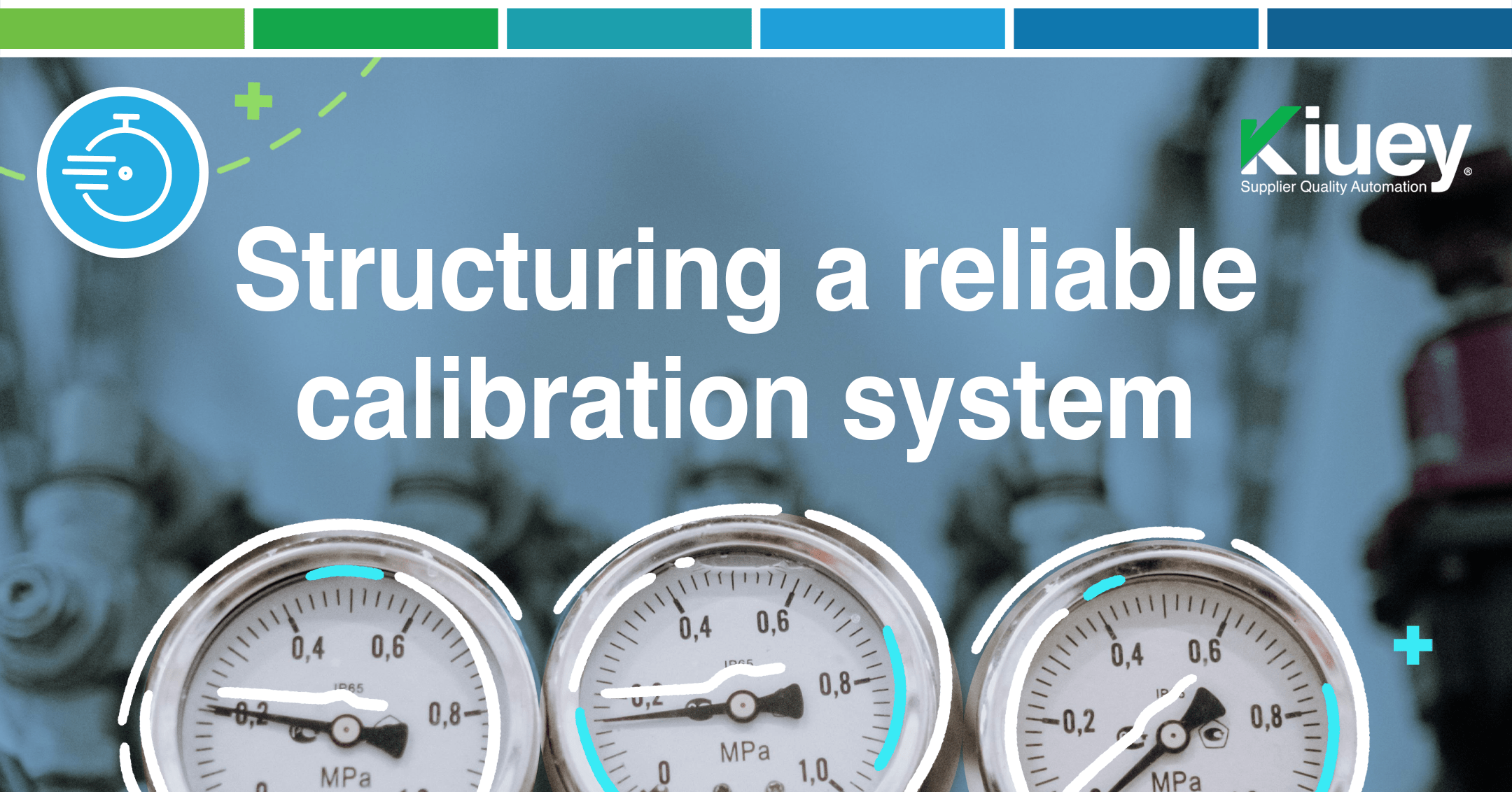
September 23, 2024
In the realm of supplier quality engineering, where precision and consistency reign supreme, there is a often-overlooked yet indispensable hero: calibration. It’s the unsung guardian of quality, the silent sentinel ensuring that measurements are accurate and reliable.
Imagine a world without it. Measurements would be like a ship adrift on a stormy sea, tossed about by waves of uncertainty. Products would be inconsistent, safety compromised, and trust eroded.
It is more than just a technical process; it’s a commitment to excellence. It’s a promise to customers that products will meet their expectations, a reassurance to regulators that safety standards are being met, and a testament to a company’s dedication to quality.
The Importance of Calibration
Calibration is crucial for several reasons:
- Accuracy and Precision: It ensures that measurement instruments provide accurate and reliable readings, which is essential in industries where even small errors can have significant consequences.
- Compliance: Many industries are subject to strict regulations that require regular calibration of equipment. Failure to comply can result in fines and penalties.
- Quality Control: Consistent practices help maintain quality control throughout the supply chain by ensuring that measurements are accurate.
- Efficiency: Using calibrated equipment can improve operational efficiency by reducing rework and scrap.
- Safety: In industries such as healthcare and aerospace, proper calibration is essential for safety. Faulty measurements can lead to dangerous situations.
- Data Integrity: Calibration ensures that the data collected is accurate and reliable, which is essential for informed decision-making.
- Traceability: A good system allows for traceability, meaning that measurements can be traced back to recognized standards.
- Cost-Effectiveness: While there may be upfront costs associated with establishing a calibration system, in the long run, it can save money by minimizing errors and improving efficiency.
Best Practices
To ensure the effectiveness of your system, consider the following best practices:
- Develop a Plan: Create a comprehensive plan that outlines the frequency of calibration, the equipment to be calibrated, and the procedures to be followed.
- Use Accredited Laboratories: Whenever possible, use accredited laboratories to perform calibrations.
- Maintain Records: Keep detailed records of all calibrations, including the date, results, and any corrective actions taken.
- Regularly Review and Update Your System: Periodically review your calibration system to ensure that it remains effective.
- Provide Training: Ensure that all relevant personnel are trained on calibration procedures and the importance of using calibrated equipment.
By following these best practices, supplier quality engineers can establish a robust system that supports product quality, safety, and compliance. A well-managed calibration program is essential for maintaining a competitive advantage and building trust with customers.
Let's talk to see how PPAP Manager can help your company to save time and money.