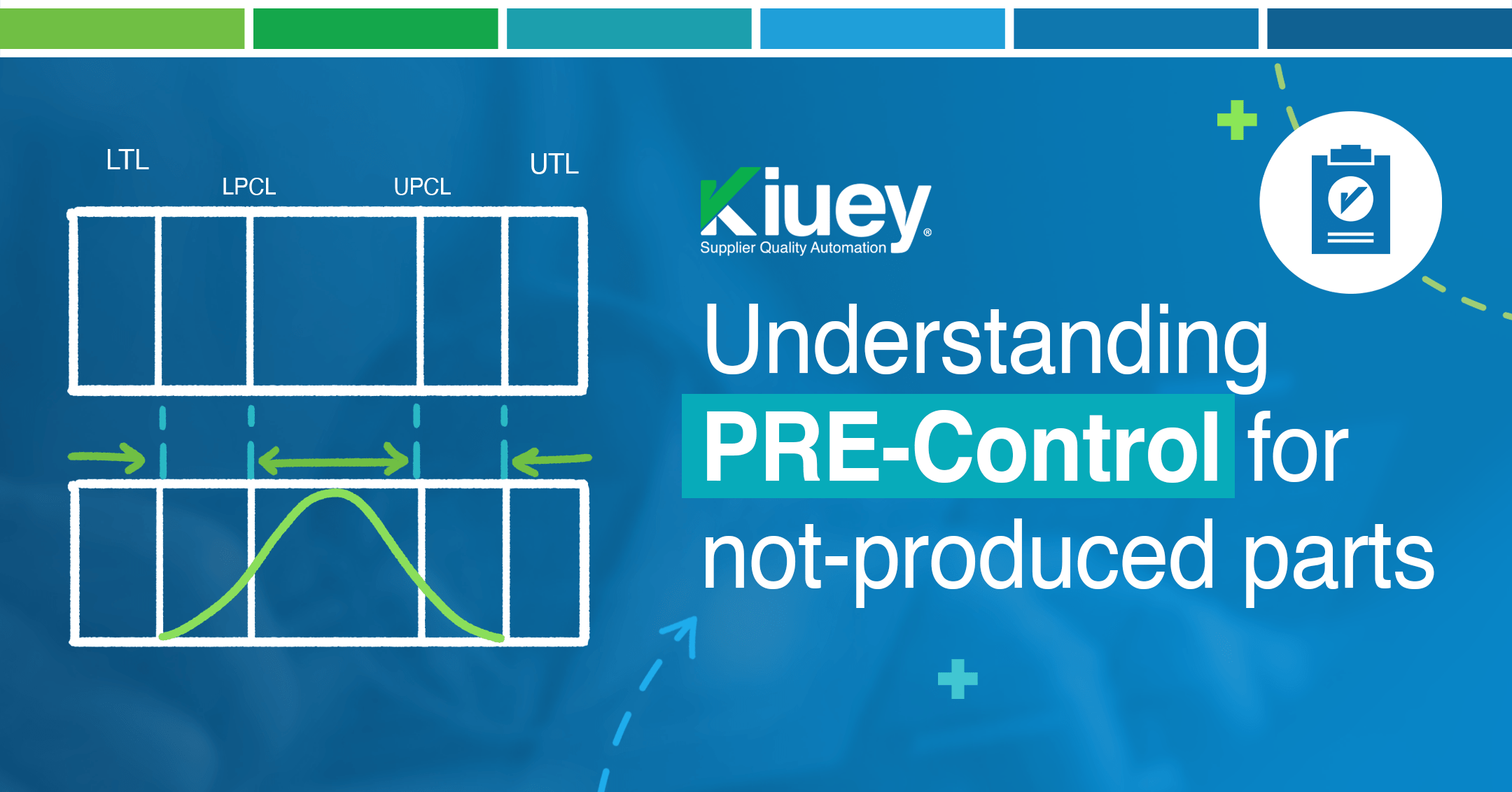
September 26, 2024
In the world of manufacturing, ensuring product quality is paramount. One effective tool for achieving this is PRE-Control. This technique empowers shop operators to maintain process control and prevent the production of defective parts.
Unlike statistical process control (SPC), which requires a significant amount of data before drawing conclusions, this technique provides immediate feedback, making it highly responsive to process signals.
Understanding PRE-Control
- Tolerance Zones: PRE-Control divides the drawing tolerance into three zones: Green, Yellow, and Red. The middle half of the tolerance is the green PC zone.
- Cpk and Probability: If a process’s Cpk is 1.0, meaning the tolerance equals 6x sigma and the process mean coincides with the tolerance mean, we can expect 86% of readings to fall within the green zone and 7% in each of the yellow zones. This leads to a low probability of false alarms, making this a reliable tool.
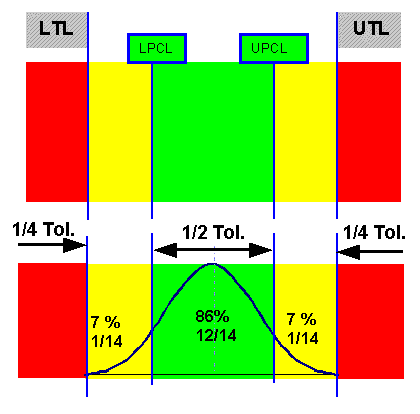
Reference of PRE-Control Zones. Source: SymphonyTech
PRE-Control Rules
- Set-up Qualification: To qualify a set-up, five consecutive pieces must be in the Green zone. Any yellow or red readings require process adjustment.
- Sampling: After qualifying a set-up, sample two consecutive pieces. If both are green or one is yellow and the other is green, continue production. If both are yellow on the same side, adjust the process. If yellows are on opposite sides, investigate the process further. A red reading triggers process adjustment and inspection of parts produced since the last sampling.
- Impact of Cpk: The probability of qualifying a set-up with five consecutive green readings decreases as Cpk values decrease. This demonstrates its effectiveness in identifying and addressing process capability issues.
Gauging
To simplify its application, color markings can be incorporated into gauging tools. These markings visually indicate the different zones, making it easier for operators to identify and respond to process variations.
Conclusion
PRE-Control offers a simple yet powerful approach to ensuring product quality. By providing immediate feedback and empowering operators to make timely adjustments, it helps prevent the production of defective parts. While not a substitute for control charts, this is a valuable tool for maintaining process control and improving overall product quality.
Let's talk to see how PPAP Manager can help your company to save time and money.