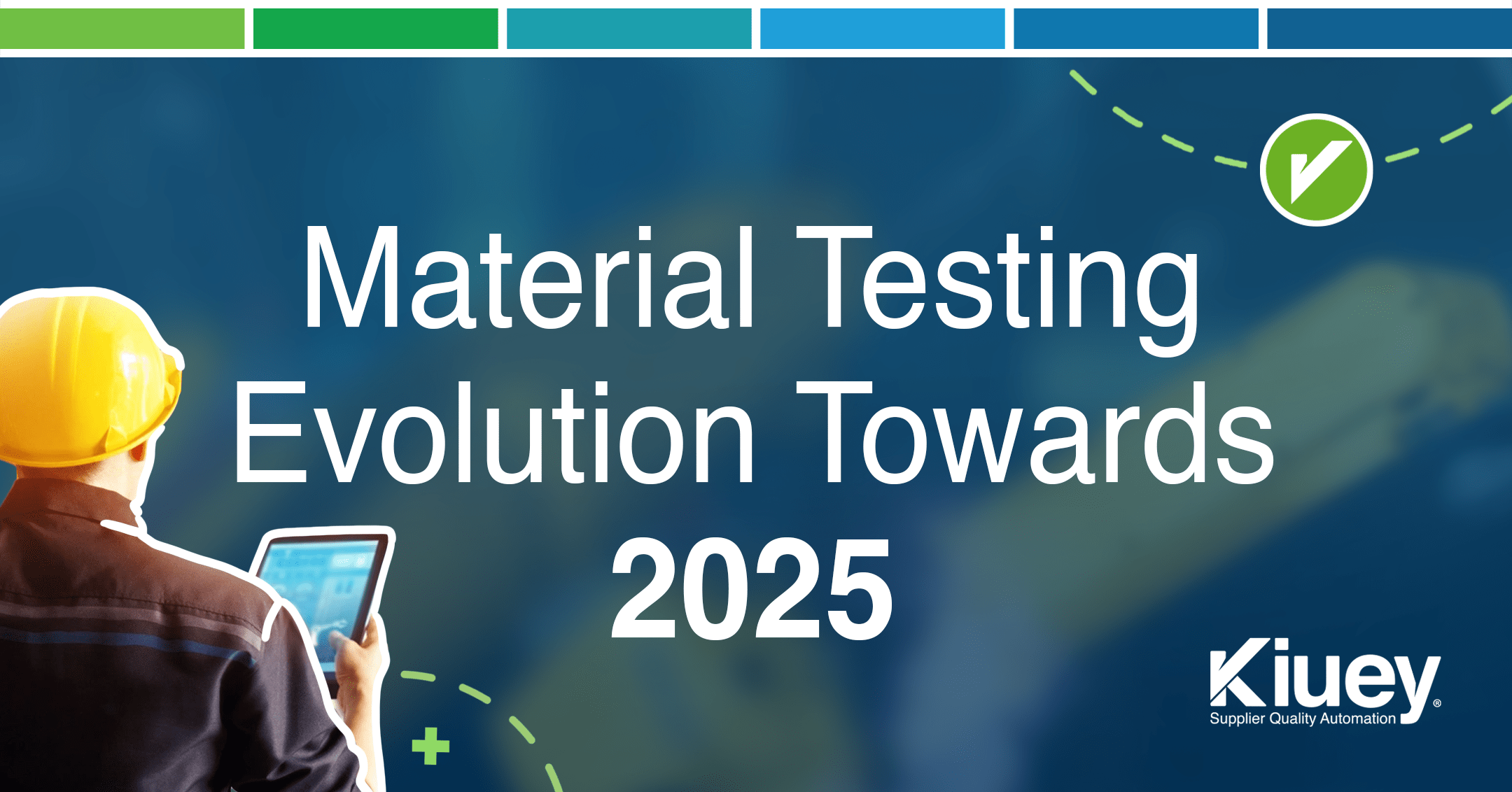
December 21, 2024
Supplier Quality Engineers (SQEs) play a critical role in ensuring the safety and efficacy of medical devices, including catheters. Their responsibilities extend beyond simply inspecting incoming materials; they must deeply understand the manufacturing processes and the rigorous testing protocols that ensure product quality. This article focuses on three key physical tests (material testing) for catheters and their significance for SQEs.
1. Tensile: A Foundation for Material Testing
Tensile testing provides crucial data on the mechanical properties of catheter materials. SQEs need to:
- Establish acceptance criteria: Based on product specifications and regulatory requirements, establish acceptable ranges for tensile strength, elongation at break, and modulus.
- Monitor supplier performance: By analyzing tensile test data from incoming materials and finished products, monitor supplier performance and identify potential issues early on.
- Drive continuous improvement: Analyze trends in test data to identify areas for improvement in the manufacturing process, such as material selection or processing parameters.
2. Lubricity Testing: Evaluating Smoothness and Glide
Lubricity is critical for successful catheter insertion and navigation. SQEs need to:
- Develop robust test methods: Collaborate with suppliers and internal engineering teams to develop standardized lubricity testing protocols that accurately reflect real-world conditions.
- Monitor coating consistency: Ensure that suppliers consistently apply hydrophilic coatings with the desired thickness and uniformity.
- Investigate performance variations: Analyze test data to identify potential root causes of variations in lubricity, such as changes in coating materials, application processes, or storage conditions.
3. Trackability Testing: Simulating Real-World Performance
Trackability testing provides valuable insights into the catheter’s performance in a simulated clinical environment. SQEs need to:
- Review and approve test protocols: Ensure that the testing methodology accurately simulates the intended use of the catheter.
- Analyze test data: Evaluate test results to identify potential issues, such as excessive insertion forces, difficulties in navigating complex pathways, or problems with device deployment and retrieval.
- Provide feedback to suppliers: Communicate test results to suppliers and collaborate with them to implement corrective and preventive actions to address any identified issues.
Conclusion
A thorough understanding of material testing methodologies is essential for SQEs. By actively participating in the development and implementation of these tests, SQEs can effectively:
- Assess supplier capabilities: Evaluate the quality and consistency of incoming materials and finished products.
- Identify and mitigate risks: Proactively identify and address potential quality issues before they impact patient safety.
- Drive continuous improvement: Collaborate with suppliers to optimize manufacturing processes and enhance product performance.
By embracing these responsibilities, SQEs can play a vital role in ensuring the delivery of high-quality, safe, and effective catheters to patients worldwide.
Disclaimer: This article is for informational purposes only and should not be considered medical advice.
Subscribe to our newsletter.
Your go-to destination for insights, best practices, and innovative solutions in supplier quality assurance.
Let's talk to see how PPAP Manager can help your company to save time and money.