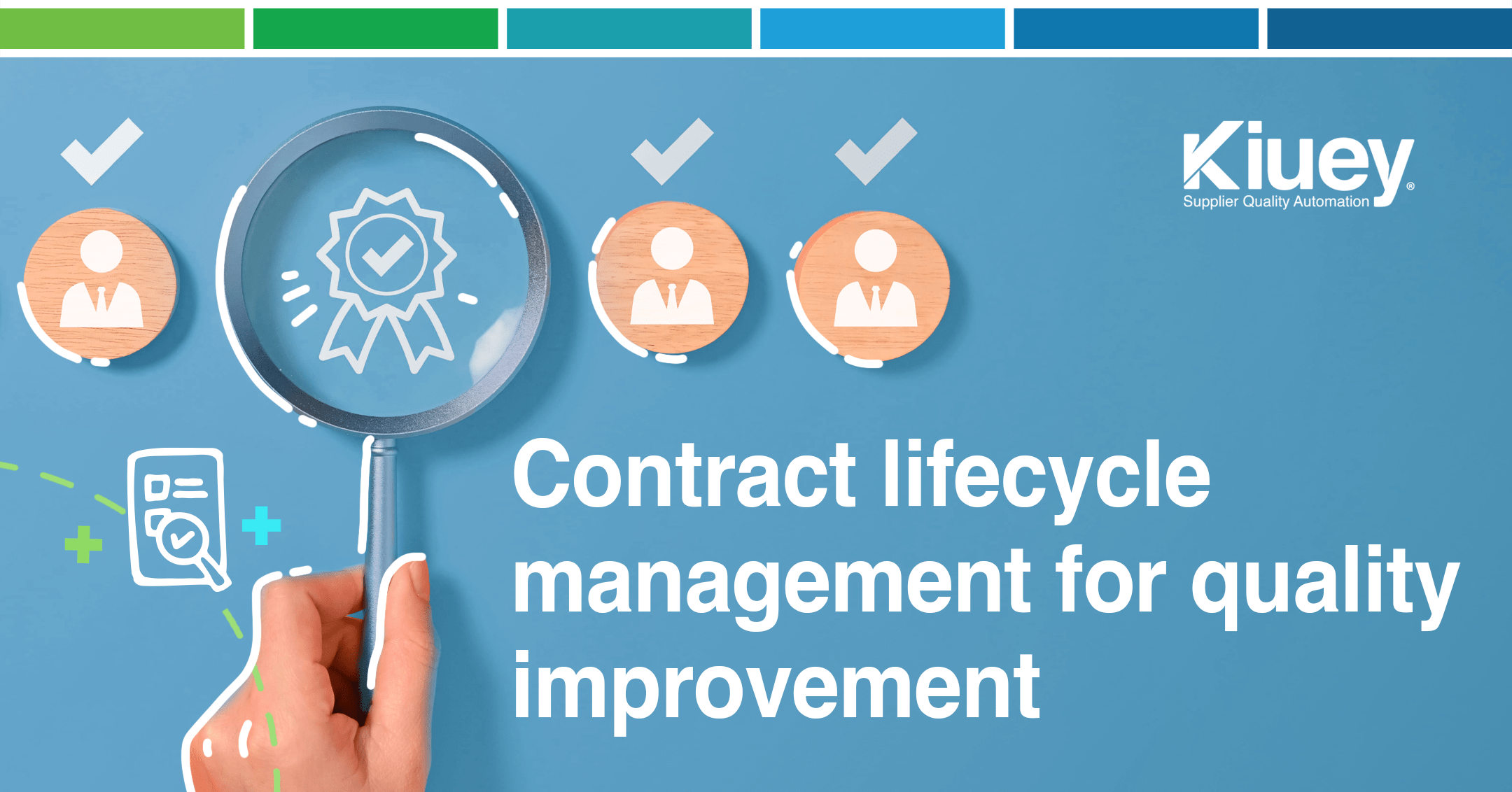
June 30, 2024
Ensuring consistent quality throughout the supply chain is a constant pursuit for organizations. Contract lifecycle management (CLM) plays a vital role in this endeavor. By implementing a robust CLM system, companies can establish a framework for collaboration, communication, and continuous improvement with their suppliers, ultimately leading to better quality products and services.
The Traditional Approach: Fragmented and Inconsistent
Historically, contract management often relied on paper-based systems and siloed processes. This fragmented approach led to inconsistencies, communication gaps, and difficulties in enforcing quality standards.
The Five Stages of the Contract Lifecycle Management:
Traditionally, contract management can be viewed through the lens of five key stages:
- Contract Creation and Authoring: This stage involves drafting the contract, ensuring it clearly defines quality expectations and outlines supplier responsibilities.
- Contract Negotiation and Approval: Negotiations may involve discussing quality control measures and defining performance metrics.
- Contract Execution and Award: Once finalized, the contract is signed and the supplier begins production.
- Contract Administration and Monitoring: This stage involves monitoring supplier performance, ensuring adherence to quality specifications.
- Contract Close-out or Renewal: The contract is reviewed, and decisions are made regarding potential renewal based on factors like quality performance.
While these stages remain essential, CLM systems offer a more integrated and efficient approach.
CLM: A Catalyst for Quality Improvement
Modern CLM systems go beyond simply storing contracts. Here’s how they contribute to quality improvement:
- Standardized Contract Language: CLM systems can enforce the use of pre-approved templates that clearly define quality expectations and responsibilities.
- Improved Communication and Collaboration: CLM platforms provide a central hub for communication with suppliers, facilitating discussions about quality concerns and improvement initiatives.
- Risk Management and Early Detection: CLM systems can analyze contracts and identify potential quality risks, allowing for proactive mitigation strategies.
- Performance Monitoring and Reporting: Real-time data on supplier performance, including quality metrics, can be tracked and analyzed within the CLM system.
- Automated Workflows and Reminders: CLM can automate tasks like sending reminders for supplier audits or inspections, ensuring timely adherence to quality protocols.
- Improved Version Control and Audit Trails: CLM systems ensure clear documentation of revisions and approvals related to quality requirements throughout the contract lifecycle.
Benefits of Leveraging Contract Lifecycle Management for Quality:
By integrating CLM into their quality management strategy, companies can reap several benefits:
- Enhanced Supplier Collaboration: Improved communication fosters a collaborative environment where both parties focus on achieving quality objectives.
- Reduced Risk of Non-Compliance: Clearer contracts and automated monitoring minimize the risk of suppliers deviating from quality standards.
- Data-driven Decision Making: Insights from performance data allow companies to identify trends and make informed decisions about supplier relationships and quality improvement initiatives.
- Increased Efficiency: Streamlined processes and automated workflows improve the efficiency of contract management, freeing up resources for other quality-related activities.
- Improved Contract Visibility and Control: Centralized contract management provides greater visibility into supplier performance and facilitates proactive quality management.
Considerations and Implementation:
While CLM offers significant advantages, successful implementation requires careful planning. Companies need to consider factors like system configuration, user training, and integration with existing quality management systems.
Conclusion:
Contract lifecycle management is no longer just about paperwork. By embracing CLM as a strategic tool, companies can foster a culture of quality with their suppliers, leading to a more robust and reliable supply chain. In today’s competitive landscape, where quality is paramount, CLM offers a valuable asset for achieving continuous improvement and success. It’s a win-win proposition that benefits both buyers and suppliers, ultimately leading to the delivery of higher quality products and services to the end customer.
Let's talk to see how PPAP Manager can help your company to save time and money.