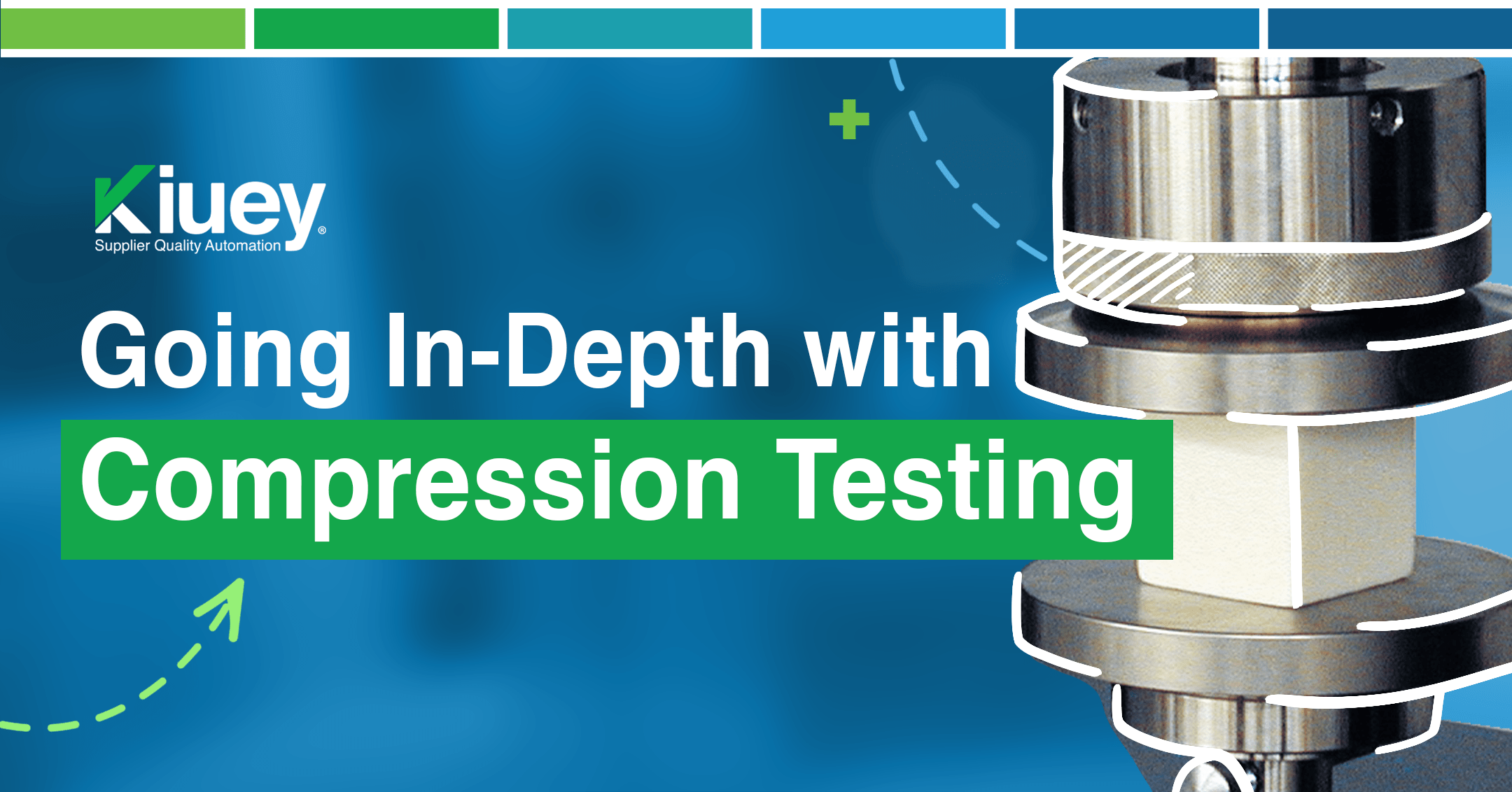
November 29, 2024
Quality control is a cornerstone of manufacturing excellence, and compression testing plays a pivotal role in ensuring product reliability and safety. As a Supplier Quality Engineer (SQE), understanding the principles and applications of compression testing is essential.
What is Compression Testing?
Compression testing is a mechanical process that subjects a material or product to a compressive load, simulating real-world stresses. By measuring the force required to deform or break a sample, engineers can assess its strength, durability, and overall performance.
Key Applications in Manufacturing
Compression testing finds applications across various industries:
- Automotive: Testing components like bumpers, seat frames, and engine mounts to ensure they can withstand impact and vibration.
- Aerospace: Evaluating the strength and fatigue resistance of materials used in aircraft structures.
- Consumer Goods: Assessing the durability of products like toys, electronics, and household appliances.
- Pharmaceuticals: Verifying the hardness and friability of pills to ensure consistent dosage.
- Packaging: Determining the load-bearing capacity of containers and packaging materials.
Critical Parameters in Compression Testing
To obtain meaningful results, SQEs should focus on these key parameters:
- Peak Load: The maximum force applied to the sample before failure.
- Strain: The deformation of the sample under load.
- Modulus of Elasticity: A measure of the material’s stiffness.
- Yield Strength: The stress at which the material begins to deform plastically.
- Ultimate Tensile Strength: The maximum stress a material can withstand before breaking.
Selecting the Right Test Method
The choice of test method depends on the specific product and its intended use. Common compression testing methods include:
- Static Compression: Applying a constant load to the sample until failure.
- Dynamic Compression: Applying a cyclic load to simulate real-world conditions.
- Creep Testing: Measuring the deformation of a material under a constant load over time.
- Stress Relaxation Testing: Monitoring the decrease in stress over time in a sample under constant strain.
The Role of SQEs in Compression Testing
SQEs play a crucial role in ensuring the quality and reliability of products. Key responsibilities include:
- Reviewing Test Plans: Ensuring that test plans are comprehensive and align with product specifications.
- Monitoring Test Procedures: Verifying that tests are conducted according to established procedures.
- Evaluating Test Results: Analyzing test data to identify trends and potential issues.
- Collaborating with Engineering Teams: Working closely with engineers to optimize product designs.
- Implementing Corrective Actions: Taking steps to address any quality problems identified through testing.
By understanding the principles and applications of compression testing, SQEs can make informed decisions to improve product quality, reduce costs, and enhance customer satisfaction.
Subscribe to our newsletter.
Your go-to destination for insights, best practices, and innovative solutions in supplier quality assurance.
Let's talk to see how PPAP Manager can help your company to save time and money.