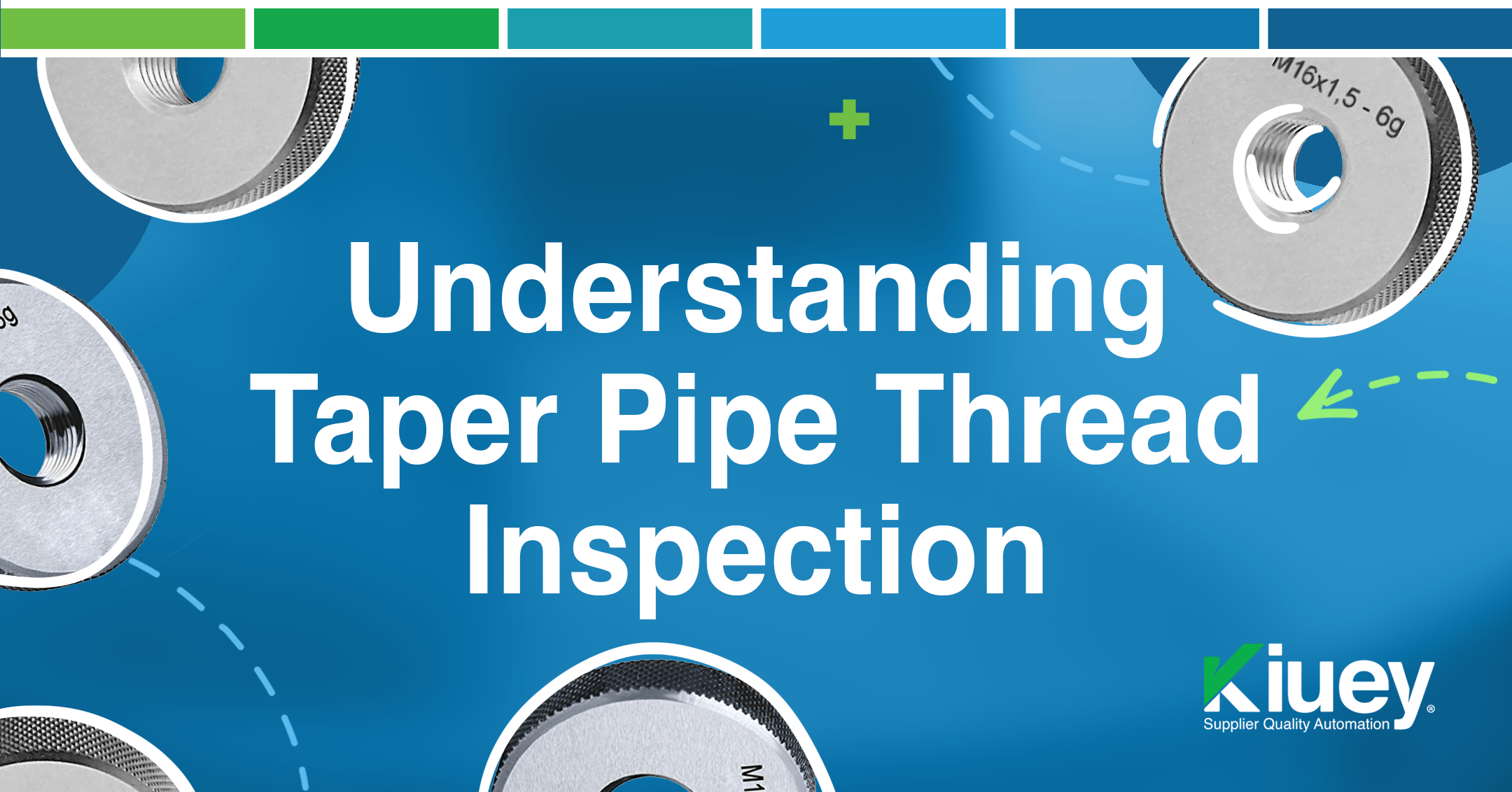
December 23, 2024
National Pipe Taper (NPT) threads are a common type of tapered pipe thread widely used in various industries, including plumbing, hydraulics, and gas lines. These threads are crucial for creating leak-tight connections, ensuring proper system functionality, and maintaining safety.
Understanding NPT Threads
- Tapered Design: NPT threads are characterized by a consistent taper along their length. This taper ensures a tight seal as the male and female threads are joined, creating a leak-proof connection.
- 60-degree Thread Angle: NPT threads have a 60-degree included angle, a common standard in many thread forms.
- Key Features: Critical dimensions include thread diameter, pitch, taper angle, and thread length.
The Role of Supplier Quality Engineers (SQEs) on Thread Inspection
SQEs play a vital role in ensuring the quality and reliability of components with NPT threads. Their responsibilities include:
Defining Inspection Criteria:
- Establishing clear and concise inspection criteria based on industry standards (e.g., ANSI/ASME B1.20.1) and customer requirements.
- Specifying acceptable tolerances for thread dimensions, taper, and other critical parameters.
- Determining appropriate inspection methods, such as thread gauges, micrometers, and visual inspection.
Supplier Audits:
- Conducting regular audits of suppliers to assess their thread inspection capabilities and ensure compliance with established quality standards.
- Evaluating the effectiveness of the supplier’s quality control systems, including their use of appropriate tools, equipment, and trained personnel.
First Article Inspections:
- Performing thorough inspections on the initial production run of parts to verify conformance to specifications.
- Documenting all inspection results and identifying any deviations from the agreed-upon requirements.
In-Process Thread Inspection:
- Monitoring production processes at the supplier’s facility to ensure consistent thread quality.
- Identifying potential issues early in the manufacturing process to prevent defects.
Data Analysis and Corrective Actions:
- Analyzing inspection data to identify trends, root causes of defects, and areas for process improvement.
- Collaborating with suppliers to implement corrective and preventive actions to address any identified nonconformances.
- Working with suppliers to develop and implement continuous improvement initiatives.
Importance of Proper NPT Thread Inspection
- Leak Prevention: Ensuring leak-free connections is critical for safety, especially in applications involving hazardous fluids like gas.
- Product Reliability: Proper thread quality contributes to the overall reliability and longevity of the final product.
- Customer Satisfaction: Delivering products with high-quality connections enhances customer satisfaction and builds long-term relationships.
- Cost Savings: Identifying and preventing thread defects early in the supply chain reduces costs associated with rework, scrap, and warranty claims.
- Safety Compliance: Adhering to industry standards and regulations related to thread quality is essential for ensuring product safety and avoiding legal and regulatory penalties.
Conclusion
SQEs play a critical role in ensuring the quality and reliability of components with NPT threads. By establishing robust thread inspection procedures, conducting thorough supplier audits, and collaborating effectively with suppliers, SQEs can minimize the risk of defects, improve product quality, and enhance customer satisfaction.
Subscribe to our newsletter.
Your go-to destination for insights, best practices, and innovative solutions in supplier quality assurance.
Let's talk to see how PPAP Manager can help your company to save time and money.